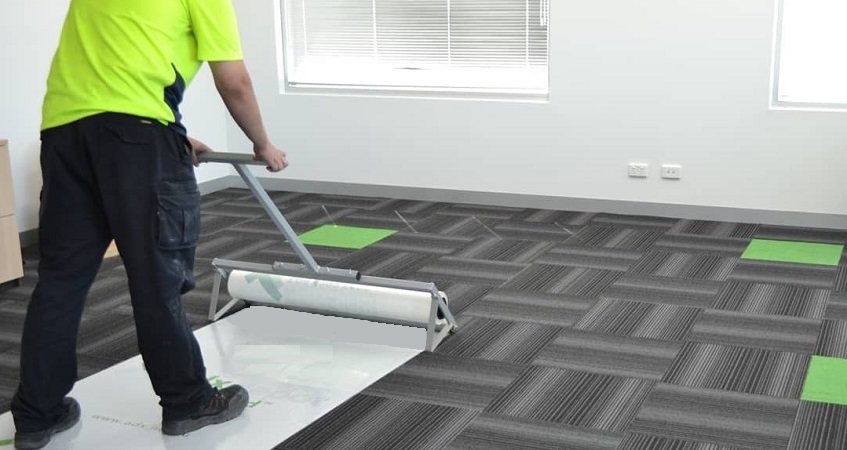
Protection Films: Types, Applications and Benefits for Safeguarding Surfaces
How can you effectively prevent scratches, spills, and damage to objects during construction, renovation, or transport? – With the help of protective films. These specialised films have become indispensable components across various industries, offering temporary yet significant protection against damage. What are the benefits of these sophisticated solutions for surface protection?
Contents
Types of Protective Films
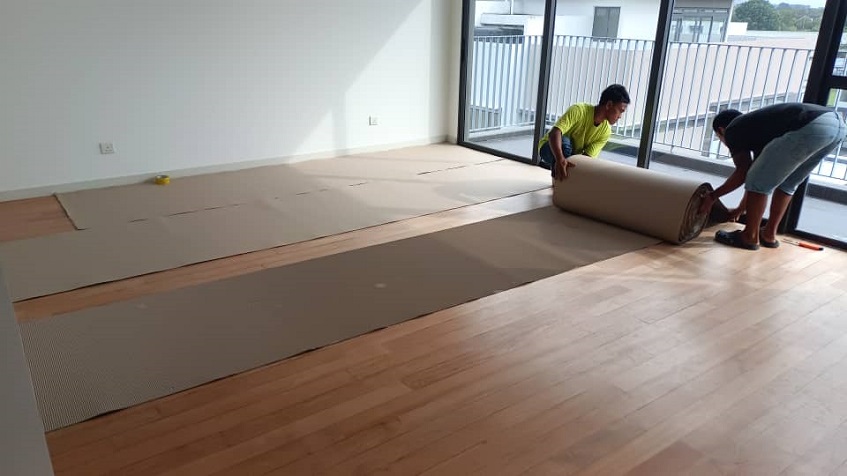
These specialized films come in various types, each designed to protect specific surfaces while maintaining their integrity.
- Polyethylene (PE) films offer an excellent balance between protection and cost-effectiveness. They come in various thicknesses and adhesion levels, making them suitable for protecting anything from gentle electronics to very robust construction materials.
- Polyvinyl chloride (PVC) offers greater durability and chemical resistance, making it ideal for more demanding applications where exposure to harsh conditions is expected.
- Polyethylene terephthalate (PET) films provide exceptional transparency while maintaining strong protective properties, which makes them suitable for applications requiring optical clarity, like display screens and glass surfaces.
Application-Specific Solutions
Different surfaces require specific film characteristics to ensure optimal protection without damage upon removal. In metal surfaces, a combination of moderate adhesion and conformability is required to prevent corrosion and scratching during processing and transport. Glass and polished surfaces demand films that are strong enough to remain intact during handling but gentle enough to remove without leaving residues. In the case of plastic substrates, manufacturers should select films that won’t interact chemically with the substrate, preventing chemical migration or surface damage.
Floor Protection Film
Protective films for floors are engineered with different thicknesses and adhesion levels to suit hardwood, vinyl, tile, and concrete substrates. These films include impact resistance to protect against damage from tools and equipment but retain slip resistance for safety purposes. Most well-formulated protection films have vapour barrier features to prevent moisture damage during curing and painting processes. They can sustain heavy foot and equipment traffic while guarding against scratches, spills, and stains.
Carpet Protection Film
Crucial protection during construction and renovation projects, carpet protection film is made of a self-adhesive material that adheres firmly to the carpet fibres without leaving unwanted residue after its removal. The film provides a waterproof barrier against paint spills, dust, or construction debris’ getting onto the carpet, allowing foot traffic without damage. Under normal conditions, these films hold up for at least 45 days, providing sufficient coverage for long-term projects.
Stainless Steel Protection Film
Stainless steel surfaces need specific protection during manufacturing, shipping, and installation. These films provide excellent adhesion while preventing residue transfer. Their UV-resistant properties prevent adhesive baking, ensuring clean removal even after long-term solar exposure. They offer protection against scratches and fingerprints while preventing chemical exposure.
Glass Protection Film
The challenge with glass protection arises from its delicate nature and its transparency requirements. Protection films for glass surfaces come with higher impact resistance coupled with optical clarity. These films provide protection from scratching, mortar splattering, and welding spattering during construction, while also allowing enough visibility for handling. Advanced glass protection films also contain UV inhibitors that prevent degradation of the glass and have unique adhesives that will not interfere with subsequent window treatments or tinting applications.
Industrial Applications
Protective films have an important role in the production process for manufacturing industries. These films are used by manufacturers of vehicles for the protection of vehicle components during assembly and shipping stages, while electronic manufacturers rely on them to keep their sensitive components undamaged until final assembly. The construction industry also applies the same films to ensure that windows, countertops, and flooring remain undamaged throughout the building process, while the aerospace industry uses specialized high-performance films to protect critical components during the manufacturing and assembly of aeroplanes and spacecraft.
What are the Benefits of Protection Films?
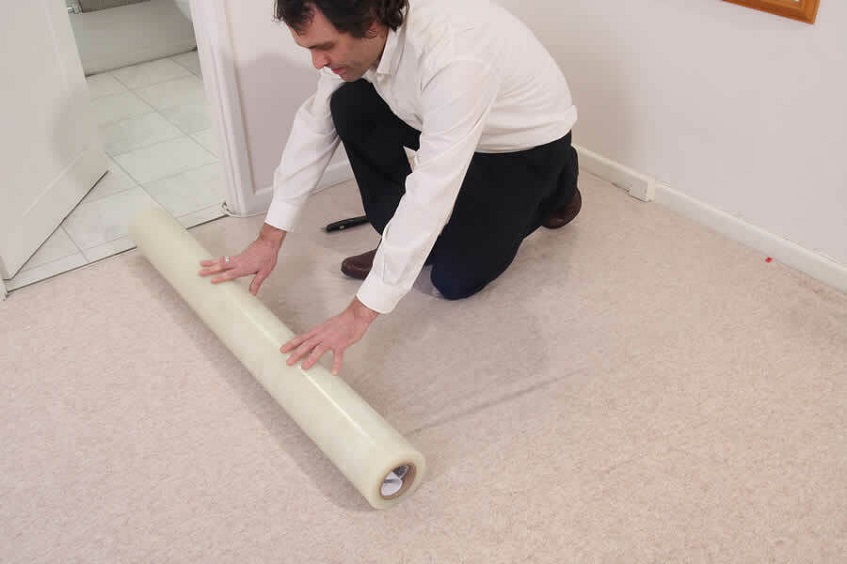
Protection films offer multiple advantages across industries:
- Reduced cleanup time and costs
- Prevention of expensive surface damage
- Better workplace safety due to slip resistance
- Environmental advantages through surface preservation
- Cost-effective alternatives to traditional methods of protection
Installation and Removal Techniques
The key to successfully applying a protection film lies in selecting the appropriate type for each surface and executing an adequate installation. The selection should be driven by factors such as the duration time of the project, working environment, and traffic level. While these films are an upfront cost, they usually save you money by preventing damage to expensive surfaces and reducing cleaning up post-project.
Installation and removal of protective films is a crucial step in the process to ensure reliable protection without harming the underlying surface. Professional installers use specialized tools and techniques for a bubble-free application with adequate tension. Different types of films will require a different film removal technique – some need a specific temperature range when removing, or a specific angle to prevent adhesive residue or surface damage.
Takeaway
Through careful material selection, proper application techniques, and ongoing technological advancement, protective films continue to play a vital role in preserving surface quality across numerous industries. As manufacturing processes become more sophisticated and surface protection requirements more demanding, the importance of these specialized materials will only increase, driving further innovation in the field.
Sorry, the comment form is closed at this time.